Peter Joeckel, with more than thirty years in the ERP business helping companies select and implement software solutions, is in a unique position to offer alternative solutions for “tried and failed” ERP software selection and implementation strategies. Whether you’re in the middle of a challenged implementation or just beginning to research available resources, contact Peter and the TurnOnDynamics team today.
The 20/80 Rule for Manufacturing ERP Software Implementations
Implementing ERP software is hard. Implementing manufacturing ERP software is even harder. With our tried and true approach, it doesn’t have to be.
There is a lot of great ERP software available for mid-sized manufacturing companies that is packed full of features and capabilities. It has been like that for the majority of my more than thirty year career helping companies with their selection and implementation projects.
Starting my career, fresh out of engineering school, implementing tier-1 manufacturing software suitable for Fortune 500 companies, I received an immediate education on the wide range of complex functionality available in these solutions. My second lesson was how impossible or incredibly expensive it was to implement.
I moved from Price Waterhouse to my own practice in 1986 when my idea to start a mid-market manufacturing practice was given a thumbs up with the caveat that a partner had to run it. As a twenty something year old know-it-all, I did not agree with that assessment.
My plan was predicated on the amazingly complete set of accounting, distribution, and manufacturing functionality found in some of the first DOS-based, mid-market offerings such as Macola and Syspro.
What I quickly figured out was that most of that functionality was overkill for the typical mid-market manufacturing company. That insight led to the highly successful model of selling and implementing “black-hole” manufacturing systems. In a “black-hole” manufacturing system you know what your inventory is at all times in its three critical stages:
- Raw materials or parts
- In-process or being worked on
- Finished widget–ready to sell
Note: a widget is a hypothetical item used to discuss manufacturing concepts. A completed widget could be a little red wagon as an example. The inventory parts that go into the red wagon might be:
- Wheels
- Axels
- Bed
- Handle
- Various nuts, bolts and other hardware
What you “lose” in the “black-hole” manufacturing model is most significantly:
- Where exactly are we in the process of making a specific widget
- Broken down by material labor and overhead, what is my exact cost structure to build a widget
- Advanced scheduling and capacity analytics
Without getting overly complicated, manufacturing software builds on two fundamental building blocks:
- The Bill of Material or BOM
- The Bill of Labor or BOL or Routing
The BOM uses the list of inventory parts it takes to manufacture a widget and creates a logical tree structure that shows us exactly how the parts come together to make a completed widget.
Creating a BOM is mostly science. A list of parts can be combined in multiple ways to make different finished products. The BOM for our little red wagon must be exact so that you make the desired product correctly. For example, you would not put handles where the axels should go and vice versa.
The Routing defines the people, machines and tools needed to “make” or manufacture the widget.
It is my experience that a typical mid-sized manufacturing company has the information needed to create an accurate BOM readily available. They probably don’t have accurate BOM’s but they do have the information. The difference is important.
That same mid-sized manufacturing company will have almost none of the information needed to create useful routings. More importantly, they do not realize the time and effort needed to create and maintain useful and functional routes.
This fact is carefully ignored in the sales cycle much to everyone’s detriment (with the probable exception of commission based salespeople). It is my experience that mid-sized manufacturing is sold exactly and specifically on features and functions that will never be implemented!
Here is my suggestion to any small and mid-sized manufactures looking for a new ERP software solution: the information that you will gain implementing a “black-hole” manufacturing solution will give you 80% of the information you can realistically manage and afford for 20% of the time, effort and cost of implementation and maintenance. With that solution up and running you have two options:
- Run forever with this model because it gives you all the information you need or can afford
- Use this model as a logical building block to use as a stepping stone for more complex functionality that will get you 20% more information but at 80% of the implementation and maintenance cost.
For a realistic evaluation of your manufacturing ERP needs and how to employ these principals in your selection and implementation processes, please give us a call.
We can show you how a rapid implementation of an enterprise level ERP solution can dramatically save and make you money.
ABOUT THE AUTHOR
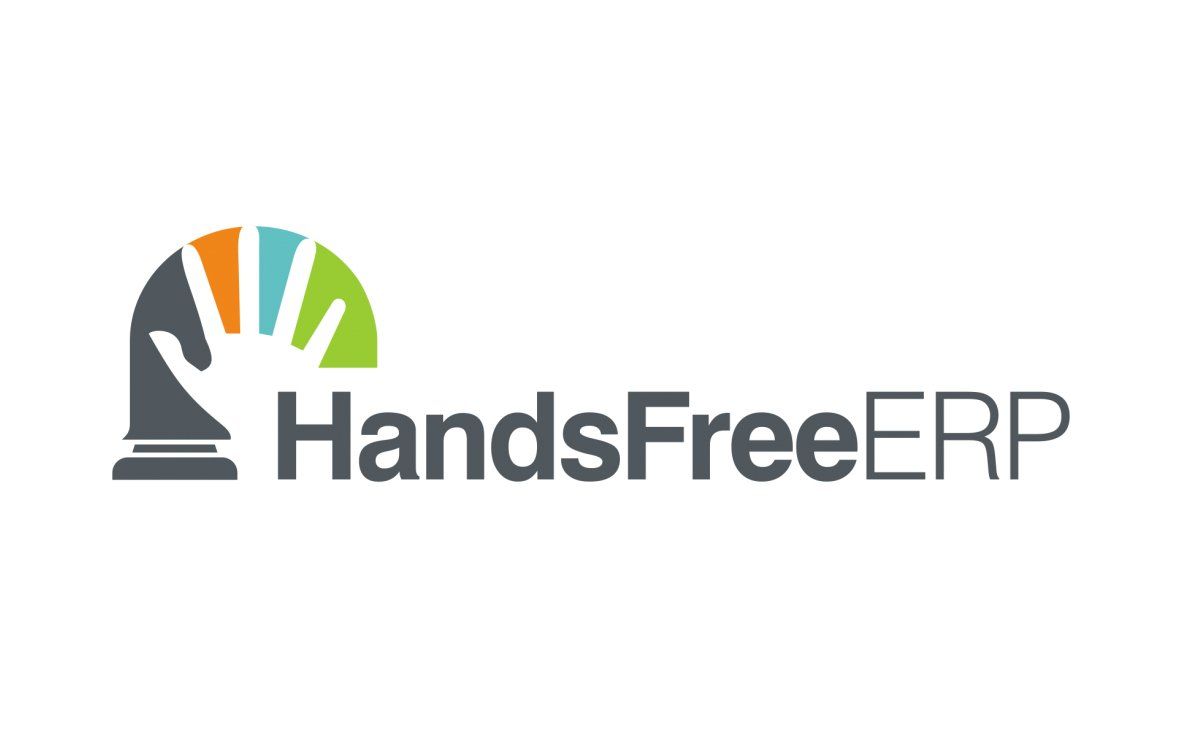
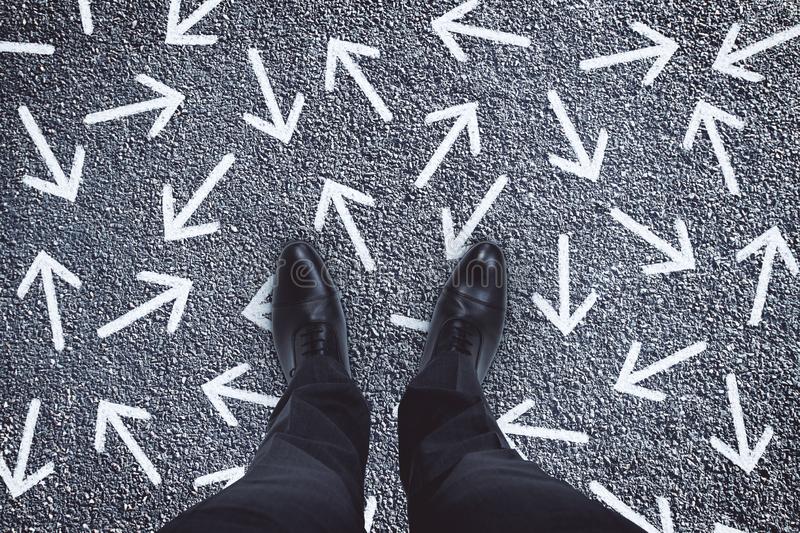
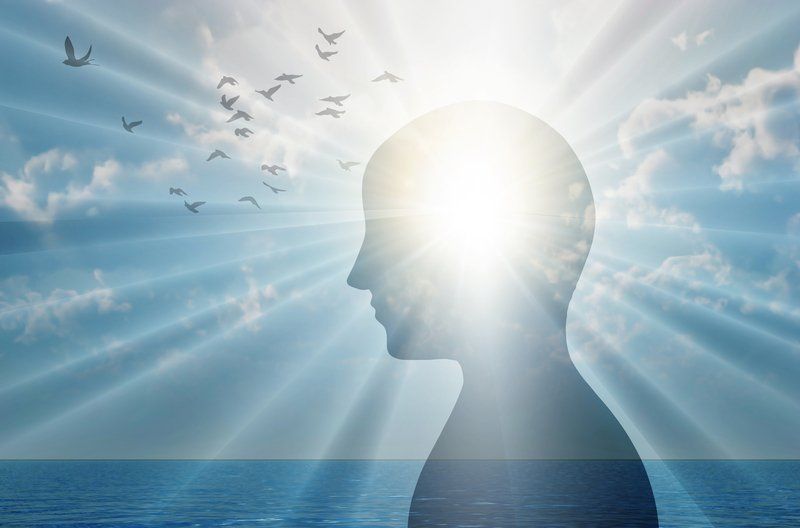
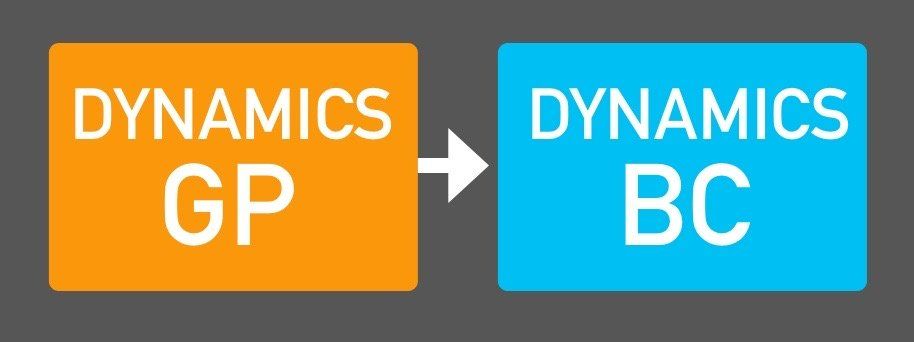